UPM Fray Bentos: más que una planta de celulosa, un enorme complejo industrial
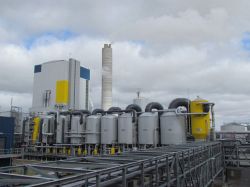
En Perspectiva visitó el edificio de la planta de celulosa UPM en Río Negro. Se trata de una de las cuatro industrias que tiene la empresa en el mundo. En diálogo con Eugenio García, gerente de recursos humanos de UPM y Matías Martínez, gerente de comunicaciones de la compañía, los especialistas explicaron que "toda la madera que ingresa a la planta sale como celulosa o como energía". En este sentido, "una planta como esta tiene la capacidad de producir una cantidad de energía que excede sus necesidades en el doble. Nosotros estamos generando en el entorno de los 130 megavatios". La planta en Uruguay es la más grande que tiene UPM y corresponde a que "la escala permite mayor eficiencia en los costos e inversiones que, de otra forma, se harían muy difíciles".
(emitido a las 11.11 Hs.)
EMILIANO COTELO:
Este edificio tan moderno y tranquilo en el que estamos ubicados esta mañana dentro del predio de UPM, en el departamento de Río Negro, es apenas la fachada de un enorme complejo industrial.
Cuando en mayo de 2006 vinimos aquí con el equipo de En Perspectiva por primera vez, las obras de construcción estaban avanzadas pero todavía faltaba más de un año para que la fábrica de pasta de celulosa se pusiera en funcionamiento.
Ahora, cuando la planta ya lleva más de tres años de actividad y cuando está produciendo al 100 % de su capacidad, nuestra visita de este fin de semana nos permitió apreciar en todas sus dimensiones el tamaño y la complejidad de este emprendimiento, que incluye la planta de celulosa, una usina generadora de energía eléctrica, otras empresas proveedoras de productos químicos, el sistema de grandes piletas para el tratamiento de efluentes, varios depósitos y un puerto techado para despachar la celulosa en barcazas rumbo a Nueva Palmira.
Para conocer un poco mejor lo que ocurre en este predio de 500 hectáreas, vamos a conversar con el ingeniero Eugenio García, que fue gerente de producción cuando esto era Botnia, y hoy es gerente de recursos humanos de UPM. También nos acompaña Matías Martínez, gerente de comunicaciones de UPM.
En primer lugar, ubiquemos en pocas palabras qué es UPM.
MATÍAS MARTÍNEZ:
UPM es una empresa líder en el sector forestal y de papel. Tiene tres áreas de negocios bien diferenciadas, que son todo lo que hace a la energía y la celulosa por un lado, en el cual nos ubicamos nosotros. Luego, todo lo que concierne al sector de papel. La empresa produce distintos tipos de papeles: finos, de revista, especiales, y todo lo que hace a los materiales transformados, es decir, las etiquetas, los RFID y los compuestos de madera contrachapada.
EC - ¿Cuántas plantas de celulosa tiene UPM en el mundo?
EUGENIO GARCÍA:
Cuatro plantas, contando la de Fray Bentos. UPM fue una empresa de tradición papelera, y está cambiando en ese sentido. Está creciendo en los sectores de negocio de la energía y de la celulosa y de los materiales transformados, mayormente para agregarle valor a todo lo que viene de la forestación.
EC Entonces, el origen de UPM es más bien papelero. Estaba en la etapa final de todo el proceso. Ella misma no fabricaba la celulosa.
EG - Fabricaba, pero era simplemente un insumo necesario para su fin, que era la producción de papel, y en ello era en lo que era más destacada. Es una de las principales empresas productoras de papel del mundo. Pero ahora está haciendo de la celulosa y de la energía, que van de la mano en muchos sentidos, un negocio en sí mismo, y allí está creciendo.
EC - Veamos la celulosa, producción principal de esta planta. ¿Qué es este producto?
EG - La mitad de los constituyentes de la madera son fibras. Aquí se produce el proceso de sulfato, craft, y se blanquea. Nuestra celulosa es de eucalipto blanqueada, producida por el proceso craft.
EC - ¿De qué tipo de eucalipto viene?
EG - En el caso de nuestra planta en Uruguay tenemos dos grandes variedades que hacen el gran porcentaje del suministro; el grandis y el dunnii. Pero también utilizamos globulus, viminalis, maidenii y otras especies en pequeñas cantidades.
EC Después, aquí la madera y los chips provenientes de esas variedades de eucaliptos se mezclan.
EG - Se mezclan en una receta, lo cual es fundamental, porque de los porcentajes que se utilizan de las distintas variedades resultan las propiedades finales de nuestra fibra, y, por ende, las propiedades finales del papel que la utilice como insumo.
EC - Quedó dicho al pasar pero me parece importante puntualizarlo: ¿de esta planta de celulosa de UPM en Fray Bentos sale un único tipo de celulosa?
EG - Un único tipo de celulosa.
EC - ¿Siempre?
EG - Siempre.
EC - ¿No hay cambios previstos, momentos del año en que se produce una y momentos en que se produce otra?
EG - Para nada. Ese es un sistema de producción que se utiliza en otras plantas en el mundo. Por definición, en el diseño del proyecto ya definimos que queríamos hacer un único producto de determinada calidad y llegar a la excelencia en esa calidad.
EC - ¿Para qué se utiliza esa celulosa?
EG - Básicamente para papeles de fotocopia, de impresión...
EC - El papel A4, que uno usa con tanta frecuencia.
EG Exactamente. Ese papel, que cada día está más en nuestras vidas y en nuestros hogares, es uno de ellos. Y papeles de revista, que sufren procesos posteriores. Por ejemplo, papeles estucados, para los que también se utiliza una base celulósica.
EC - ¿A qué mercados se destinan? ¿Adónde van esos paquetes de celulosa que salen de acá? ¿Pasan a Nueva Palmira y de allí van al mundo?
EG - Básicamente al este asiático y a Europa. Los porcentajes varían entre 60 y 40%, y van alternándose según las situaciones de mercado. En principio, el proyecto estaba diseñado para suministrar 60% de nuestra celulosa a Europa y 40% a Asia.
EC - Esta es una fábrica que elabora 1.100.000 toneladas de pasta de celulosa por año. Eso implica más de 3.000 toneladas por día.
EG - Exactamente.
EC - ¿Es la más grande que UPM tiene en el mundo? ¿Por qué se dio esta circunstancia?
EG - Es un tema de escala. A medida que se van construyendo nuevas plantas, estas tienden a ser un poco mayores porque la escala permite mayor eficiencia en los costos e inversiones que, de otra forma, se harían muy difíciles. Por ejemplo, todas las inversiones que tienen que ver con el cuidado ambiental y que son sumamente costosas. En una planta de mayor escala se facilitan. No es casualidad que tengamos los mejores indicadores ambientales en el mundo, incluso mejores que los de las plantas que están en Finlandia. Eso proviene de esta escala que nos permite hacer las inversiones necesarias para tratar los efluentes de la manera que los tratamos.
EC Cuando se construía esta planta ustedes destacaron que está hecha con las mejores tecnologías disponibles, eso que en inglés se denomina con la sigla BAT. ¿No ha habido mejores tecnologías desde que la planta de UPM se diseñó, construyó y se abrió en 2007?
EG - Las guías que componen las BAT no han cambiado desde entonces. Siempre están en revisión, y es probable que en corto plazo cambien algunas indicaciones. De todas formas, nosotros estamos muy por encima de lo que nos piden esas guías. Esas guías dirigen hacia dónde uno tiene que ir en cuanto a indicadores ambientales, pero no establecen ni una tecnología ni un valor muy preciso. Más bien habla de rangos. En todos los indicadores estamos mejor que el mejor de los rangos de las BAT. Aun cuando hubiera cambios en las BAT, seguramente vamos a seguir estando en la punta durante mucho tiempo.
EC - Se trata de un sistema altamente automatizado. Si uno recorre el proceso de fabricación de la celulosa encuentra pocos operarios. ¿Cómo es esto?
EG - Para obtener la calidad que obtenemos y para tener la estabilidad en el proceso que se requiere para nuestros clientes, es necesaria la automatización. Más todavía para una planta que tiene esta capacidad productiva, que es muy grande.
EC - ¿Dónde están los 800 empleados que se supone que habitualmente andan por acá?
EG - Eso es muy importante. No hay pocas personas. Tal vez el tamaño relativo de los equipamientos hace parecer que hay pocas. El hecho de que sea automatizado hace que el personal no esté directamente trabajando en forma manual sobre los equipos sino en la sala de control, donde están todos los equipos computarizados que permiten el control a distancia de los equipamientos. Esto tiene una cantidad de ventajas; no solo en el control y la calidad del producto y en la estabilidad del proceso, sino también en la seguridad del personal. Es muy distinto interactuar con un proceso a distancia mediante computadoras que tener que hacerlo manualmente, como antiguamente se hacía.
***
EC - Desde la audiencia preguntan qué significa la marca UPM. ¿Es una sigla?
EG - Fue una sigla. Hoy ha perdido un poco ese sentido. Quiere decir United Paper Mills. Surgió de la asociación de varios productores de papel que dieron lugar a esta empresa.
EC - Hablamos de la producción de celulosa, pero en este predio hay otras actividades. Una de ellas, que para muchos puede haber sido una sorpresa, es la generación de energía eléctrica a partir de biomasa. ¿Desde siempre se ha dado en el mundo esta complementación entre producción de celulosa y generación de energía eléctrica?
EG No. Ya tiene unos cuantos años pero no es desde siempre. Las plantas antiguas desechaban como efluente aquella parte de la madera que no era celulosa, a veces incluso sin tratar. Estamos hablando de 70, 80 años atrás. Hoy la utilizamos para la generación de energía.
EC - ¿Cuál es ese producto?
EG - Ese producto es el cemento que mantiene unidas las fibras de celulosa. Se llama lignina.
EC - Rosario explicaba cómo empieza todo este proceso de fabricación de celulosa, que consiste en separa de esos chips de madera la celulosa por un lado y la lignina por otro.
EG - Exactamente. Me estoy preocupando. Están aprendiendo demasiado y nos van a sacar algunos puestos.
EC - Hay una comparación entre la madera y una viga de hormigón. ¿Cómo era eso?
EG - Es algo que ilustra y permite entender el proceso de producción de celulosa conceptualmente. La madera se comporta como una columna o viga de hormigón; las fibras de celulosa son las varillas de hierro y la lignina y otros componentes que están en menor cantidad hacen las veces del cemento pórtland que las mantiene unidas. El proceso de producción de celulosa consiste, conceptualmente, en la disolución de ese cemento para liberar las fibras de celulosa.
EC - ¿Qué pasaba antes con la lignina?
EG - Lamentablemente se desechaba. Tiene un poder calorífico muy interesante y esa capacidad de ser aprovechada para el uso energético, pero se desechaba. La tecnología moderna estamos hablando de décadas atrás ha ido mejorando en eficiencia, pero ya hace muchos años que esta tecnología se utiliza para producir energía. Con la mitad de la madera que no es celulosa se produce energía. Toda la madera que ingresa a la planta sale o como celulosa o como energía.
EC - La energía que esta usina de UPM genera le permite satisfacer todos los requerimientos de producción de este complejo industrial, y la electricidad que sobra se vende a la red de UTE. ¿Siempre fue así?
EG - No, en las últimas décadas la eficiencia ha mejorado muchísimo, tanto en el uso de energía para producir toneladas de celulosa, como en la capacidad de generar energía cuánta energía uno produce por tonelada de celulosa. Hace 20 años una planta de este estilo satisfacía alrededor del 85% de sus necesidades con energía proveniente de la propia madera.
EC - O sea que tenía que comprar energía afuera.
EG Sí, o generarla por otros métodos. Generalmente se usaban combustibles fósiles. Actualmente, una planta como esta tiene la capacidad de producir una cantidad de energía que excede sus necesidades en el doble. Nosotros estamos generando en el entorno de los 130 megavatios.
EC - ¿Cómo se puede comparar eso?
EG - Es algo así como el 10 % del promedio de consumo en el Uruguay.
EC - La usina generadora de energía de UPM produce el equivalente al 10 % de todo el consumo de Uruguay.
EG Aproximadamente. Ese es un número redondo que puede dar una idea del monto de energía que producimos. De cualquier forma, hay que decir que la mitad de esa energía la consumimos nosotros mismos en el proceso de producción de celulosa. Eso es lo muy bueno que ha pasado en los últimos años: que la otra mitad es excedentaria. La usamos para dos cosas. Por un lado, para producir productos químicos. En otras plantas se traen del exterior. Nosotros los consumimos mediante una empresa tercerizada especialista en ello, que no solo nos suministra a nosotros sino que tiene capacidad de proveer a otras plantas, tanto en el país como en el exterior. Esto constituye otro rubro de exportación. El resto de la energía, algo así como un cuarto de la energía que producimos, se vuelca a la red de UTE mediante un acuerdo de ida y vuelta que tenemos: normalmente, le suministramos energía a la red, y cuando la producción de energía de nuestra planta cesa, para poder arrancar tomamos energía de la red de UTE. Es un acuerdo tipo cuenta corriente, con un gran excedente a favor de UPM, en el sentido de que normalmente nosotros proveemos a la red.
EC Para tener una idea, ¿a una ciudad de qué tamaño permite abastecer esa energía que se vuelca a la red de UTE?
EG - Estamos abasteciendo alrededor de 30, 35 megavatios, y Fray Bentos consume 11, o 12 en el pico. Si lo trasladáramos a hogares, que es un tipo de consumo porque están los consumos industriales y de otra índole, podríamos decir que suministramos energía para unos 150.000 hogares.
EC - O sea que la instalación de la planta de UPM no requirió una determinada capacidad de generación del Estado uruguayo o de UTE. UPM se las arregla por sí misma y, al mismo tiempo, suplementa a UTE, porque le vende a la red energía. De otro modo, UTE tendría que generar con maquinaria propia.
EG Exactamente. Y en aquel entonces UTE debería haberla generado con combustibles fósiles. Haber podido evitar eso también es algo favorable.
EC - ¿La venta de energía eléctrica es una línea de negocios de UPM?
EG Sí. No solo en este caso y el de las plantas de celulosa, sino que la energía como tal es uno de los rubros de negocio de UPM, que tiene plantas de generación de energía de distinto tipo y no solo las asociadas a las de celulosa.
***
EC - Rosario, más temprano tú saludaste a la gente que ahora está trabajando en la sala de control del edificio principal de UPM.
ROSARIO CASTELLANOS:
Sí, compromiso que adquirí cuando lo visité.
EC - Pero después llegó el mensaje de Carolina, que dice: "Estuve toda la noche trabajando con el turno 3 para entregarle al turno 5 la planta en condiciones impecables".
RC - No me lo comentaron.
EC - Y dice: "Ahora escucho el programa empezando a disfrutar de los cuatro días libres". Y manda un saludo para quienes están ahora, pero que se haga extensivo al turno 3.
RC - Van saludos para Carolina, entonces. El resto del edificio está impecable, así que supongo que es parte de la costumbre aquí.
EG - Es bueno comentar que Carolina está embarazada, o sea que dirige el turno en muy buenas condiciones estando embarazada.
EC - Hablemos del personal. Dijimos que son 800 los hombres y mujeres que trabajan en esta planta. ¿Cómo se distribuyen uruguayos y extranjeros?
EG - Son 99 % uruguayos, 1 % extranjeros. Eso es un orgullo.
EC - Ustedes habían pensado inicialmente que iba a haber una proporción mayor de finlandeses, por ejemplo.
EG - Quienes diseñaron el proyecto, que básicamente eran finlandeses, partían de la base de que la proporción iba a ser distinta. Pero luego la práctica les ha mostrado que el recurso humano uruguayo es excelente en su capacidad de aprendizaje, velocidad de aprendizaje, compromiso, amor a la camiseta, como la selección. Y están encantados, tanto que en este momento es al revés, no solo que acá el porcentaje de extranjeros es muy pequeño, sino que estamos enviando ingenieros y profesionales uruguayos a Finlandia, en algunos casos para procesos de mejora de las plantas finlandesas con estos ingenieros uruguayos.
EC - ¿Ellos están contados en los 800, o van aparte?
EG - Están todavía contados en los 800, porque siguen siendo parte de nuestra plantilla. Están haciendo trabajos temporales en estos proyectos que comentaba, pero muy probablemente en el futuro pasen a ser parte de algún puesto corporativo y dejen de ser puestos acá, que han de ser sustituidos por otras personas.
EC - Son profesionales uruguayos que adquirieron la formación inicial acá y ahora van a ir a trabajar en otras plantas, por ejemplo en el montaje de una planta de UPM.
EG - No solo en el montaje, sino en la mejora de las plantas ya existentes. Son ingenieros uruguayos que aprendieron de finlandeses, pero que por su capacidad y entrega los mismos finlandeses quieren llevarlos a trasmitir nuestra forma de trabajo acá en Uruguay a las plantas finlandesas para hacerlas más eficientes. Lo digo de una forma totalmente "pizarrera", como verá, con muchísimo orgullo, porque tenemos un conjunto de ingenieros y profesionales uruguayos jóvenes de la mejor calidad.
RC - Otro motivo de orgullo es, por ejemplo, que un finlandés haya elegido Uruguay para hacer su curso de verano, con este frío, y esté trabajando en este momento en la sala de control.
EG - Exactamente, hay un sistema de becas, y cuando le preguntaron adónde quería ir, se vino para acá, pudiendo disfrutar el verano del norte se vino al frío del Uruguay y está encantado.
EC - En esa misma línea, ustedes nos comentaban el caso de Gonzalo Gianbruno.
EG - Sí, que es el jefe de turno del turno 5 que está en este momento.
EC - Que ahora va a dar ¿qué tipo de paso?
EG - Próximamente va a ser director de recursos humanos para toda el área de pulpa a nivel mundial. Gonzalo es ingeniero químico, pero se inició en la época de Botnia en recursos humanos, luego ha trabajado dos años en producción y ahora está dando este salto que lleva talento uruguayo a todas las plantas de celulosa que tiene y que va a tener UPM en el mundo.
EC - Ahí tenemos a alguien que va a ser el director de recursos humanos de UPM en el área pulpa de celulosa en todo el mundo.
EG - Nada menos.
EC - Volviendo a la realidad de esta plantilla, en el complejo industrial de Fray Bentos el 99 % son uruguayos, y ¿qué pasa con el corte Montevideo-interior, Río Negro-otros departamentos? ¿Cómo son esas proporciones?
MM - Hoy en la planta el 78 % de los empleados somos nacidos en el interior del país, del departamento de Río Negro es aproximadamente el 60 % de las 800 personas que ingresan diariamente a brindar un servicio y el 23 % son personas nacidas en Fray Bentos. Y algo que parece importante destacar es que esas 800 personas hacen a la producción en la planta, pero no podemos dejar de lado que esto es una cadena productiva, es una de las partes finales de la producción, y que en toda la cadena productiva, el vivero, las plantaciones, la cosecha y el transporte, hablamos de 3.400 personas que día a día trabajamos para hacer de esto una producción competitiva. Otro dato para destacar en este aspecto es que de esas 3.400 personas 300 somos profesionales universitarios que estamos trabajando en distintos departamentos del Uruguay.
EC - ¿Tienen los datos de cuántas familias se han radicado en Fray Bentos por el emprendimiento de UPM?
EG - No.
EC - El caso de Matías es uno. Tú, Matías, vienes de Durazno.
MM - Yo soy nacido en Durazno, luego viví la mayor parte de mi vida en Montevideo y los últimos seis años antes de ingresar a la empresa estuve estudiando en el exterior. Soy uno de los que nos mudamos con la familia a Fray Bentos. Son muchos los casos de compañeros de la parte de operaciones, de ingenieros, que están radicados con sus familias. Entre 70 y 80 familias nuevas estamos insertas en la comunidad desde los años 2006, 2007.
EC - Aclaremos que UPM Botnia en su momento construyó aquí en Fray Bentos un barrio, el barrio Jardín, donde están instalados varios de ustedes.
MM - Construyó dos barrios, uno en el cual vivimos actualmente, que es un predio que consta de 70 casas y apartamentos, pero también construyó un barrio obrero, destinado a las personas que estaban construyendo la planta, que fueron 108 viviendas, que fueron todas destinadas a la Intendencia, que junto con el Ministerio de Vivienda ha definido quiénes eran las personas más necesitadas para hacer uso de ellas, lo cual generó un impacto muy positivo en ese aspecto en Fray Bentos.
EC - Hablemos del impacto ambiental de esta planta de celulosa. La puesta en marcha, la inauguración, estuvo precedida de una gran polémica en este rubro que derivó incluso en un conflicto con la República Argentina. El debate giraba en torno a la contaminación que la actividad de UPM-Botnia podría generar en el entorno. El visitante nosotros el sábado, Rosario esta mañana cuando da la vuelta por este predio puede observar, cerca del río, una serie de grandes piletas de decantación. ¿Cómo funciona ese sistema?
EG - Podemos asegurar que no hay ningún impacto ambiental, que estamos funcionando muy por debajo de todos los límites que nos ha impuesto el Estado mediante la Dinama. En ese sentido, tanto por nuestros propios análisis como por los que hace la Dinama, tenemos la absoluta certeza de estar cumpliendo con todo.
EC - En estos días se van a conocer los resultados del monitoreo conjunto Uruguay-Argentina, el primer informe del monitoreo conjunto.
EG - Aparentemente sí, nosotros en forma oficial no tenemos nada todavía. De cualquier forma, estamos muy tranquilos antes de ese monitoreo, porque hemos monitoreado el ambiente desde el año 2005 para tener una línea de base, para saber cómo estaba el ambiente antes de que nos pusiéramos en funcionamiento, y hemos continuado con ese monitoreo a lo largo de toda la vida productiva de la planta. Eso muestra claramente que no ha habido ningún impacto en el ambiente.
MM - Todos los datos son públicos, parte de la política comunicacional de la empresa es publicar todos los resultados ambientales en nuestro sitio web. Luego todas las personas que estén interesadas en conocer el proceso y esos resultados simplemente contactándonos pueden acceder a esas publicaciones que hacemos semestralmente. Y como comentaba Eugenio: tenemos la total certeza de que la planta se viene desarrollando en forma óptima y que no hay ningún impacto negativo en el ambiente.
RC - Una de las cosas que me llamaron la atención es que todo el sistema de pluviales que está previsto con los canalones a lo largo de la caminería termina en una especie de laguna anterior al bombeo. Pregunté para qué era, porque está fuera de las piletas, y me dijeron que, en caso de que la lluvia estuviera barriendo algunos productos, allí se puede realizar un tratamiento anterior a volcar esa agua de lluvia al río.
EG - Eso es fundamental, no permitir que el agua de lluvia pudiese arrastrar algo.
RC - Es muy remota la posibilidad.
EG - La posibilidad es muy remota, todos los sectores donde hay utilización de productos químicos están cercados. Pero si algo saliese de esos cercos y luego la lluvia lo arrastrase, tenemos la posibilidad, con esas piletas, de retener ese líquido y volverlo al proceso sin que llegue al río.
EC - ¿Qué pasa en esas piletas? ¿Qué se puede explicar?
EG - Básicamente tenemos dos tipos de tratamientos, primario y secundario. El primario retiene sólidos en suspensión, un poco de fibra de celulosa, arena, algo que pueda estar en suspensión en el efluente. Y el tratamiento secundario es el corazón del tratamiento de efluentes y se hace mediante microorganismos que comen toda la materia que pudiera estar en el efluente y la integran a su cuerpo. Después retenemos esos microorganismos y los mandamos a la caldera de recuperación, donde generamos la energía, los quemamos y con esa materia orgánica de los microorganismos también generamos energía.
EC - La caldera que genera energía eléctrica funciona sobre la base de lignina y de estos otros residuos.
EG - Exactamente, en una forma muy minoritaria, porque esa materia es mucho menor, pero también. De esa forma podemos decir que el 100 % de lo que ingresa como madera en la planta sale o como celulosa o como energía, ya sea por la vía directa de la lignina o por la vía indirecta de los microorganismos que retienen las sustancias disueltas en los efluentes.
EC - ¿Qué pasa con los olores, que era otro aspecto delicado? Durante la visita que hicimos el sábado, sentimos en algún momento, cuando caminábamos al aire libre al lado de las torres en las que se va produciendo la delignificación, el tamizado y el blanqueo, ese olor parecido al del coliflor, ese olor del que se ha hablado tanto, que era suave y no se percibía si uno se alejaba unos metros. ¿Cómo están controlando este otro aspecto que también había que manejar?
EG - Esta planta, que es una de las más modernas del mundo, tiene un sistema de recolección de estos gases que se generan a lo largo del proceso siempre que hay productos químicos de algún tipo que luego son quemados en la caldera de recuperación, donde también a partir de ellos se produce energía; se les retiene el azufre, que es el elemento que les da el olor. Al mismo tiempo tenemos sensores a lo largo de toda la planta que miden la concentración de esos gases, por si hubiera alguna fuga eventual, y además tenemos sensores ubicados en el final del proceso de combustión que miden la cantidad de estos gases que están saliendo, que están limitados por la legislación y se encuentran en valores muy, muy bajos.
Tenemos medición de la concentración no solo de estos gases olorosos, sino de otros componentes de los gases de combustión, en el aire de Fray Bentos. Tenemos una estación de monitoreo que mide seis parámetros que está continuamente mandando señales para la planta y para la Dinama. De modo que no solo controlamos la concentración en los efluentes, sino que así como en el frente líquido en el río, medimos la concentración de cualquier elemento en el ambiente. Podemos estar tranquilos de que el ambiente de Fray Bentos en ese sentido, el aire de Fray Bentos, es de excelente calidad.
EC - Y para rematar, en esta materia de efluentes gaseosos, ¿qué son esos humos que se ven desde lejos, y acá dentro también, saliendo de chimeneas o de otras partes de la maquinaria de la planta de celulosa?
EG - Son en su totalidad vapor, salvo el de la chimenea principal, que son los gases de combustión de una combustión común, que son básicamente anhídrido carbónico y vapor de agua. Lo bueno es que ese anhídrido carbónico es proveniente de la madera, de los árboles, que a su vez necesitan tomar el anhídrido carbónico de la atmósfera para su crecimiento. Ese anhídrido carbónico, por ende, no contribuye al calentamiento global, ya que está en circuito cerrado. Se incorpora a los árboles, nosotros quemamos parte de esos árboles en la caldera de recuperación, lo emitimos a la atmósfera, y de la atmósfera lo vuelven a tomar los propios árboles que lo necesitan para continuar con el proceso de producción. En ese sentido todo lo que tú ves es básicamente vapor.
EC - Creo que no ha quedado casi ninguna de las preguntas que desde temprano nos habían enviado los oyentes. De todos modos, si hay más consultas, pueden enviarlas, se las trasladamos a ustedes y ustedes las contestan por correo electrónico. Y está también la opción de las visitas.
RC - Ante cualquier duda, creo que la mejor forma de resolver es venir y visitar. La visita es muy instructiva y muy disfrutable.
EC - Es un nuevo tipo de turismo que se ha generado en la zona, el turismo industrial o celulósico, en este caso en particular. ¿Cuántas personas han pasado ya por estas visitas?
MM - Han pasado más de 10.000 personas de distintas partes, no solo del país sino también del extranjero, que han utilizado esa vía de la visita de los sábados. Tenemos un acuerdo con una empresa local que traslada en forma gratuita a los interesados, que deben anotarse en un callcenter, que también es local, está instalado aquí en Fray Bentos, para hacer la reserva de lugar en los coches. Hay tres turnos los sábados, por lo tanto invitamos a todos los oyentes a llamar al 45627710 para hacer su reserva y conocer nuestro predio industrial.
RC - Yo diría que es el complemento perfecto de una visita al Anglo. Tenemos la modernidad absoluta con la historia de este departamento, yo recomendaría hacer las dos visitas.
EC - Son las dos grandes huellas industriales que han pautado la vida de esta ciudad.
MM - Sin duda la vida de la ciudad ha estado atada a lo industrial. Esto es en cierta forma la continuación de lo que fue el Anglo para Fray Bentos.
***
Transcripción: María Lila Ltaif